Why we need lighter electric motors
Electric motors in various designs still are the premise of the propel/drive technology. And making things smaller and lighter still is the principle of technological progress. From vacuum cleaners to drills, printers to turntables, drones to electric vehicles; making them lighter is making life better.
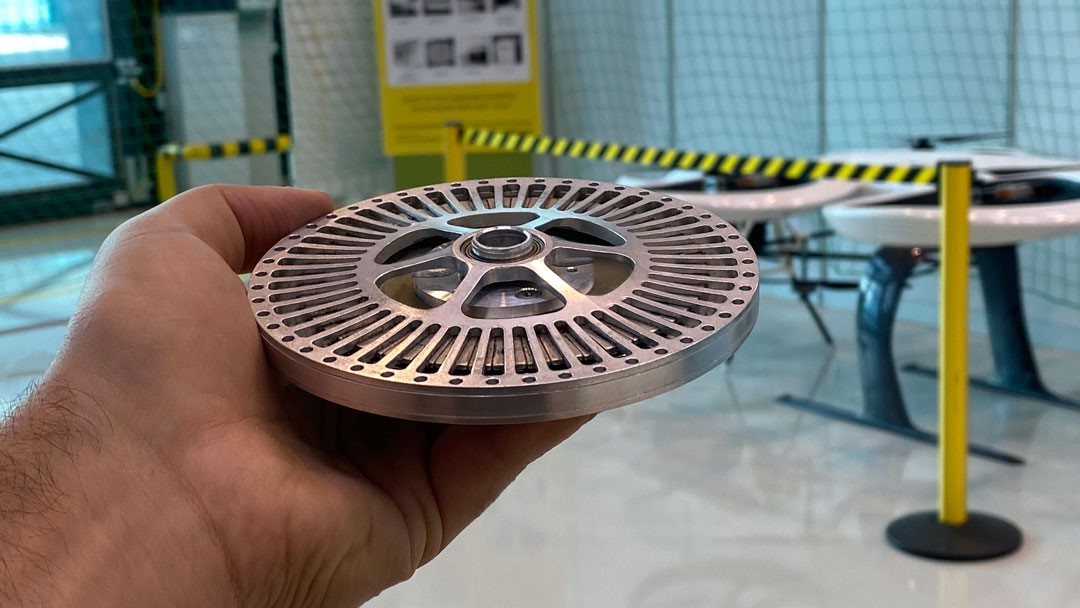
Because electric motors are mostly made of metal components, they naturally tend to be heavy, especially as they get bigger in size. This extra weight means more thrust and therefore power consumption will be required to propel or drive a vehicle. Since more power means more battery storage, this dilemma creates a cycle of adding more weight to compensate for every weight added. The only way to solve this problem is by compensating with a reduced motor size or building motors using lighter components and using innovative electric motor designs.
Our research showed that aviation companies invest 50€ on average for every gram saved! This alone points out how crucial lighter products for aerospace is.
Let's take a look at what an electric motor is and understand why electric motors are heavy through an electric motor component break-down.
Share this on:
What is an electric motor?
An electric motor, as an energy converter, transforms electrical current into mechanical movement by controlling magnetic field transition. Vice versa, it can transform mechanical motion into electrical power so they are called generators. Electric motors and generators have different electrical design; however, the physical principles of both generation processes are electromagnetic induction. In a generator, changes in the magnetic field due to mechanical motion induce current and electrical energy is produced whereas, in an electrical motor, the electrical current flowing through the conductor induces magnetic fields that lead to mechanical movement. The alternating magnetic attraction and repulsion create the premise for generating motion.
How electric motors work?
The stator and rotor are the main parts of a conventional electric motor. The term "stator" describes the immobile, still standing, part of an electric motor. The rotor, on the opposite facing side, is the moving (rotating) part of the electric motor.
The stator generally includes a core, which is wrapped in (usually copper) wires. This coil generates a magnetic field when an electric charge flows through the wires. As a result, the rotor follows the alternating magnetic field of the stator; and thus, rotates.
If the magnetic flux planar direction is parallel to the rotating axis of the electric motor, then it is called a radial flux electric motor. If the magnetic flux planar direction is perpendicular to the rotating axis of the electric motor, then it is called an axial flux electric motor. In addition to the motor type, because most electric motors are made of radial flux, the term "axial flux" is only mentioned if the motor is an axial flux electric motor. For example in our Axial Flux Permanent Magnet Brushless DC Electric Motor: AFPM-S.
The term "pancake electric motor" is very often brought together with the axial flux electric motors due to their slim, axially flat, design.
What types of electric motors are there?
There are various types of electric motors available. The power source is one way to differentiate between various types.
DC electric motors
Electric motors that work with direct current (DC), such as batteries, are classified in this type. Like most electric motors, DC motors encompass an immobile part, the stator, and a moving component, the rotor. The stator is either made of permanent magnets that continuously generate a magnetic field, or of an electromagnet that is used to induce the magnetic flux. Coils of various types are used to generate electromagnetic fields. If the coil is powered by a direct current power supply, it generates a magnetic flux and it turns into an electromagnet. The rotor is movable so that it can rotate and align with the attracting poles of the magnetic flux.
To keep the electric motor in continuous motion, the magnetic alignment must be reversed again and again. This continuous change in the electric current direction within the coil is called a pulse. If the pulse is achieved through a brush that cuts and reconnects the circuit in both directions, then we are talking about a brushed DC motor. Nowadays almost every DC motor is brushless where the pulse generation is regulated by an Electronic Speed Controller (ESC).
The changing attraction and repulsion forces keep the rotor rotating.
Brushless DC electric motors are well known for providing great torque and can be well controlled at variable speed. They are therefore preferred for rather small applications, an ideal choice for aerospace applications, drones, UAVs, electric bikes, elevators, or electric vehicles.
Asynchronous AC electric motors
Instead of DC, an AC electric motor requires an alternating electrical current. In asynchronous AC motors, turning results from electromagnetic induction of the rotor. The stator contains windings (coils) offset by a fixed angle for every phase of the current. When connected to the alternating current, coils each build up a magnetic field which rotates within the rhythm of the temporally offset line frequency. The electromagnetically induced rotor starts to rotate as it follows the magnetic path. For this reason, AC electric motors are also referred to as induction motors, as they function only via the electromagnetically induced voltage. They run asynchronously because the rotational speed of the electromagnetically induced rotor never keeps up with the rotational speed of the magnetic flux. Because of this slip, the efficiency of asynchronous AC motors is not up to that of DC motors.
Synchronous AC electric motors
With synchronous AC electric motor technology, speed is directly proportional to AC input frequency and it varies by varying the frequency. Generally, the rotor is equipped with permanent magnets rather than windings. This way, the electromagnetic induction of the rotor may be omitted, and also the rotor rotates synchronously without slipping at the identical rotational speed as that of the stator flux. Efficiency and power density are significantly higher than asynchronous electric motors.
What do Turncircles do differently: Our ultra-light axial flux permanent magnet brushless DC electric motor for every application from our scalable and stackable system
Our ultra-light permanent magnet brushless DC electric motor technology is an axial flux outrunner and provides higher torque at a less weight. This is where the seamless efficiency comes at the application level.
Why permanent magnet electric motors?
High-quality magnets are made of rare earth Neodymium metal which is a very heavy and expensive metal. However, used correctly, we can make the best out of them, because permanent magnets are very efficient energy storage devices. Once magnetized, they hold their charge for hundreds of years.
Neodymium magnet is estimated to lose around 5% of its magnetism every 100 years.
Permanent magnets provide flexibility in the electric motor design too as they can be placed independently from the power supply.
Because we want to use all the magnetic force from the permanent magnets effectively, we need to channel this force where it is needed: right next to the coil. The increased magnetic force will not only provide high torque, but it will also improve the efficiency of the motor.
To achieve this, usually, a ferric backing plate is placed behind the magnets. This iron backing plate makes the electric motor heavy.
The need for a backing plate can be avoided through the Halbach array configuration, that when permanent magnets are sequenced in a special way, the magnetic field will be concentrated on one side of the array.
Why axial flux permanent magnet electric motor?
Axial flux electric motor design is the consequence of maximizing the torque of the electric motor. At the same time, it supports the magnetic field concentration against the stator.
Axial flux permanent magnet BLDC motors are therefore expected to generate more torque per weight compared to other electric motor designs.